Eco Insight energy monitoring identifies £42,000 cost saving for UK manufacturer
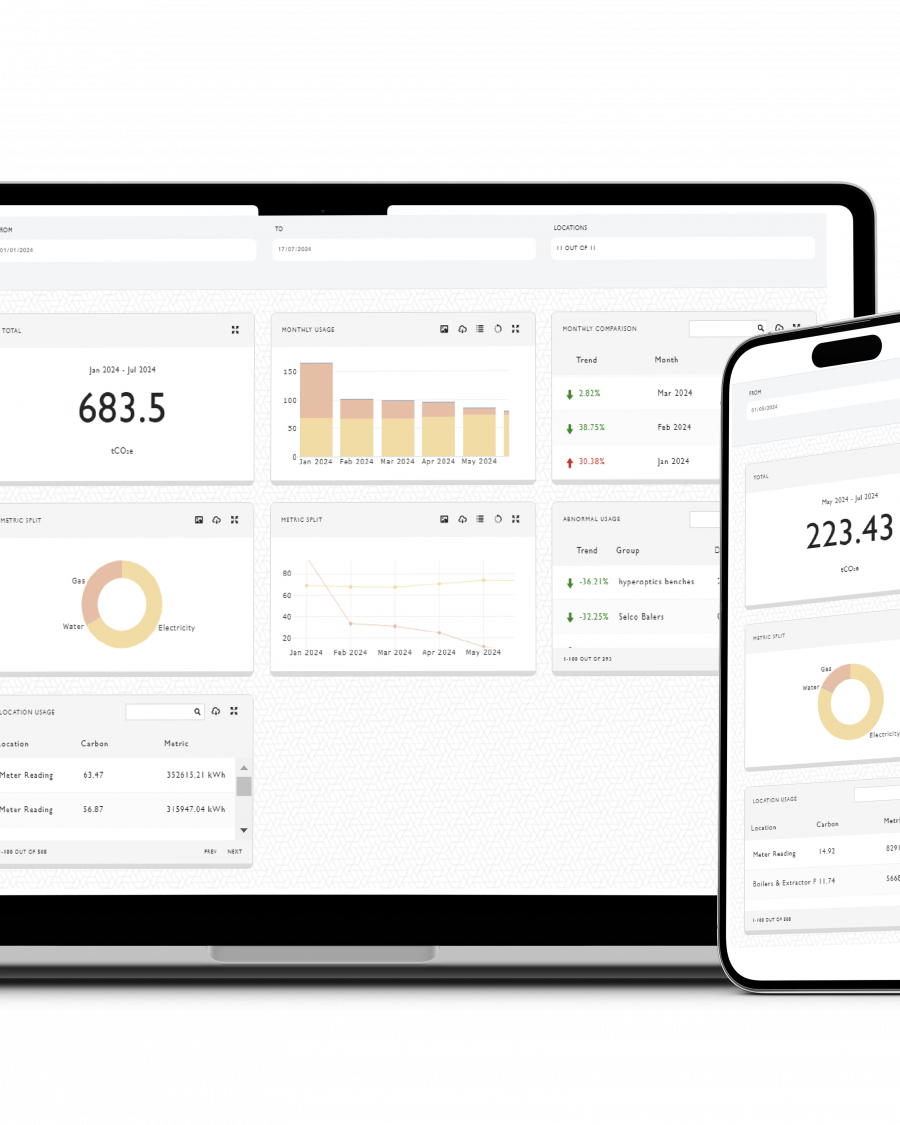
£42,000
Identified cost saving
The Impact
The implementation of Eco Insight resulted in:
- £10,858 delivered cost saving over a 12-month period
- 35,028 kWh energy consumption reduction over a 12-month period
- A further £32,000 of cost savings from 153,300 kWh of energy efficiencies identified as part of an ongoing sustainability plan for the business.
Eco Insight enabled Hyperbat to identify disproportionately-high energy costs being driven by an needlessly narrow temperature threshold inside a climate controlled area of our operation in use 24/7.
“Real-time data visualisation enabled us to quickly identify that high energy consumption was being driven by the system continually heating or cooling to maintain a -/+ 2°C temperature tolerance.
“Live EV batteries and cells do not need to be controlled to this level so we were able to extend the temperature to a 2-5°C variance which enabled the temperature in the room to fluctuate more, within the specific thresholds for stored components, significantly reducing the frequent and costly intervention of the climate control system.Paul Day, Safety, Health & Environment & Production Lead at Hyperbat
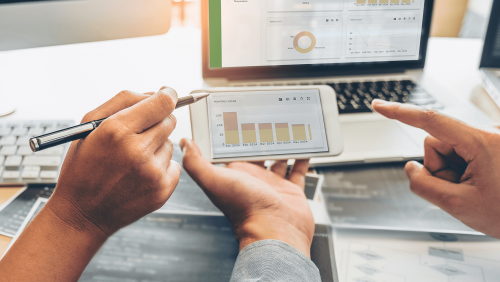
Contact us now
Get in touch to see how Eco Insight can improve the energy efficiency of your buildings and equipment