July 2024 – In the highly competitive aerospace industry, achieving optimal production operation efficiency has become a critical challenge for aircraft Original Equipment Manufacturers (OEMs). In this blog, Chris Dixon explores the multifaceted aspects of production efficiency, why it is more crucial now for Primes than ever before and what strategies Primes can employ to enhance their production processes.
Optimising Production Operations for Aircraft OEMs paper download here.
Background of the challenge of production operation efficiency for aircraft OEMs
The aircraft manufacturing safety certification process extends far beyond the mere approval of the aircraft itself. It examines the entire supply chain, scrutinising each component’s origin, fabrication, and integration. This scrutiny has ensured that travelling by air is one of the safest ways to get from A to B for decades.
This certification-led safety model makes any deviation from established suppliers or production processes extremely difficult. Moreover, the prolonged operational lifespan of aircraft, spanning upwards of three to four decades, leads to a monopoly for suppliers with limited alternatives for sourcing these parts. Consequently, aircraft suppliers have significant control over pricing and availability when compared to other industries. Aircraft manufacturers face significant challenges if suppliers become financially distressed, and experience poor delivery performance and low-quality parts.
Why is production efficiency more important now to Primes than ever before?
The aerospace industry is witnessing a significant surge in demand for both commercial and military aircraft, fuelled by two primary factors: the post-pandemic recovery of both business and leisure travel, but also the increased need for fleet modernisation. The latter is critically important both to the cost base of the Airlines, but also to their operational carbon reductions too. As the airlines and defence organisations become increasingly concerned about these impacts, the Primes face the critical challenge of enhancing production efficiency within their manufacturing and supply chains to meet these demands in a timely manner.
What can Primes do to address this? 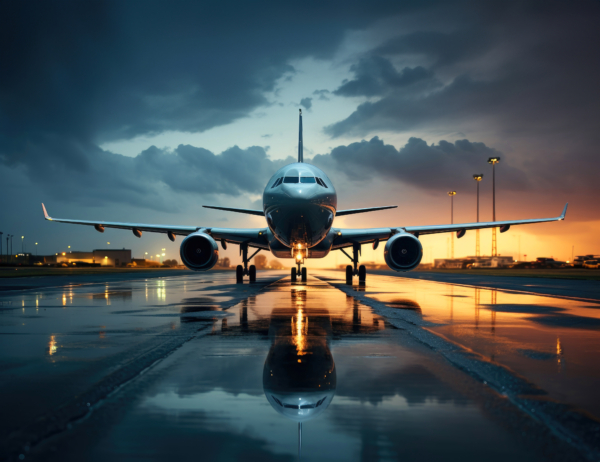
We have worked across aerospace Primes and in their supply chains to deliver significant transformation programmes, enabling production efficiency and resilience to be achieved. Our approach and insights blend the best practices learned and evolved both within and outside of aerospace.
By implementing the appropriate digital tools to provide visibility and seamless communication between the supply chain and the Prime, stronger partnerships can be built, with greater confidence that the market will deliver. Key players in the aerospace industry are identifying suppliers below the first tier of vendor networks and using data, analytics, and data-sharing models to get a complete view of the supply chain.
Embedding advanced manufacturing techniques and operational excellence into both the supplier and final assembly processes can unlock significant improvements in efficiency. Our experience in delivering similar efficiency programmes to support the industrialisation of the automotive industry and other complex manufacturing such as alternative heating and modular buildings has taught us how to ensure this is successful. By embedding lean manufacturing principles into operations, colleagues can quickly understand how to identify opportunities to eliminate waste and improve process cycle times.
Supplier Performance Management
Supplier performance management becomes an imperative, particularly in contexts where the freedom to switch suppliers is constrained. Within this framework, suppliers traditionally receive feedback regarding their delivery timeliness and product quality on a consistent basis. Nonetheless, there exists a notable gap in the extent to which aircraft manufacturers actively engage in facilitating the enhancement of supplier capabilities by providing expertise to help suppliers improve.
Exceptions to this occur when supplier performance metrics or financial indicators deteriorate to such an extent that aircraft manufacturers are forced to intervene. Aircraft manufacturers might resort to acquiring struggling suppliers outright, thereby ensuring the continuity of supply. This underscores the evolving dynamics of supplier relationships within the aerospace industry, where collaboration and intervention become indispensable tools for sustaining operational continuity and elevating overall performance standards.
Collaborative Partnerships
Establishing a collaborative partnership between Aircraft OEMs and suppliers holds the promise of mutual benefit, particularly in enhancing several critical areas: demand visibility, product quality, and supplier performance. Within this relationship, OEMs stand to gain from the assurance of receiving an adequate supply of parts conforming to the right quality standards, ensuring the fulfillment of production requirements. From this, suppliers stand to benefit from reduced waste, diminished rework efforts, minimised stockpiling of finished goods, and decreased Work In Progress (WIP) inventory levels.
Summary
Aircraft OEMs face significant challenges in maintaining production operation efficiency due to stringent certification processes and an intricate supply chain. The long operational lifespan of aircraft, often exceeding 30 years, leads to a near-monopoly for certain suppliers, limiting alternatives for sourcing parts. Suppliers wield significant control over pricing and availability, and any financial distress or poor performance on their part can severely impact aircraft manufacturers. Although alternate suppliers exist, scaling up production to meet demand is time-consuming.
With increasing demand for commercial and military aircraft, driven by post-pandemic recovery and fleet modernisation needs, production efficiency has become crucial. Airlines and defence organisations seek to replace older, less efficient aircraft with new models for better fuel efficiency, reduced emissions, and advanced technologies.
Primes must enhance production and supply chain efficiency to meet this demand by quickly incorporating new technologies like automation. Collaboration within the supply chain, using digital tools for visibility and communication and investing in advanced manufacturing techniques, can unlock greater value and improve resilience.
Download our white paper
Our white paper provides insight into the challenge of achieving optimal production efficiency for aircraft OEMs. This paper explores:
- The multifaceted aspects of production efficiency, exploring why it is more crucial now for Primes than ever before
- The strategies Primes can employ to enhance their production processes
- A case study of how Unipart Consultancy achieved a remarkable 16% uplift in Overall Equipment Effectiveness (OEE) for a major aerospace manufacturer
- Supplier performance management, focusing on improvements in sustainability and the implementation of sustainable sourcing practices to ensure long-term operational efficiency and environmental responsibility.
Download our white paper on achieving optimal production efficiency for aircraft OEMs here.
Your journey to supply chain sustainability
If you’re looking for more support in sustainable aviation, or need help with your supply chain’s sustainability journey, get in touch with us at Unipart Consultancy. Contact us here.